
Guide pillars
Guide pillars play a crucial role in press tools by ensuring precise positioning and form the basis for guiding moving components. They contribute to maintaining stability, precision, and durability of the entire tool. Various types of guide pillars are available to meet specific application requirements.
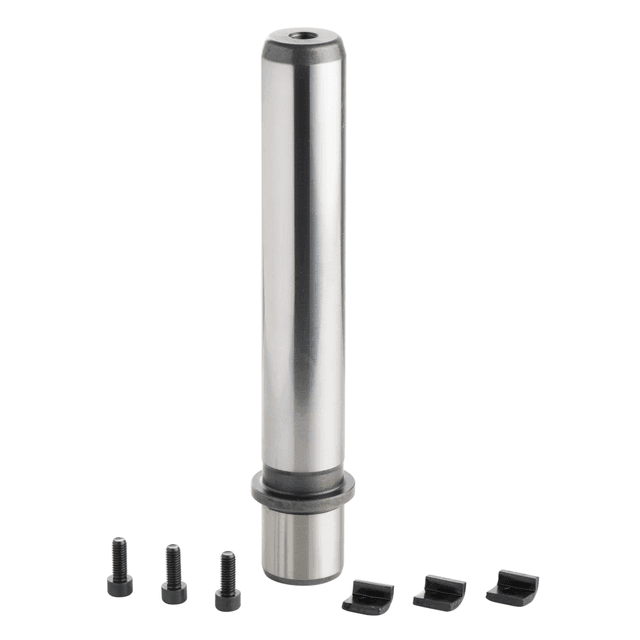
Demountable guide pillar with mounting clamps P21 - ISO 9182
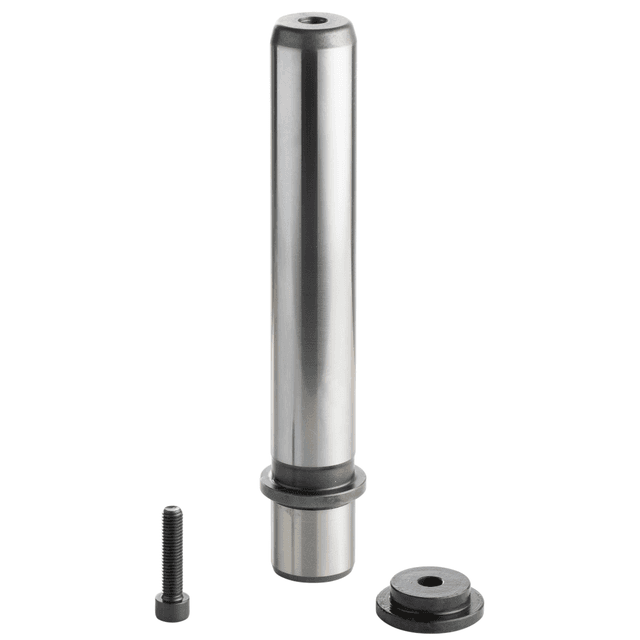
Demountable guide pillar with central fixing P22 - ISO 9182
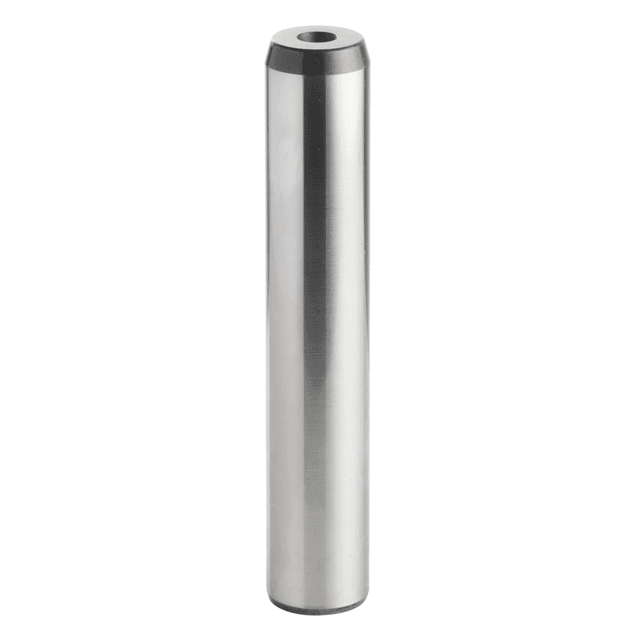
Guide pillar P10 - ISO 9182
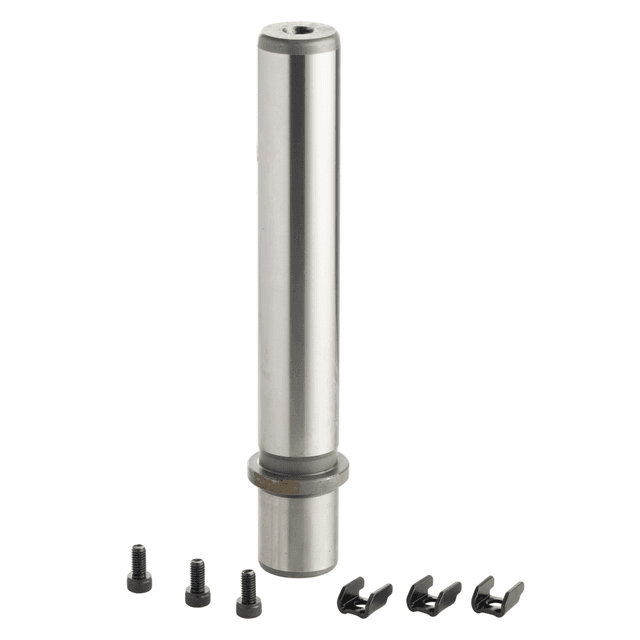
Demountable guide pillar with mounting clamps DP21 - DIN 9825
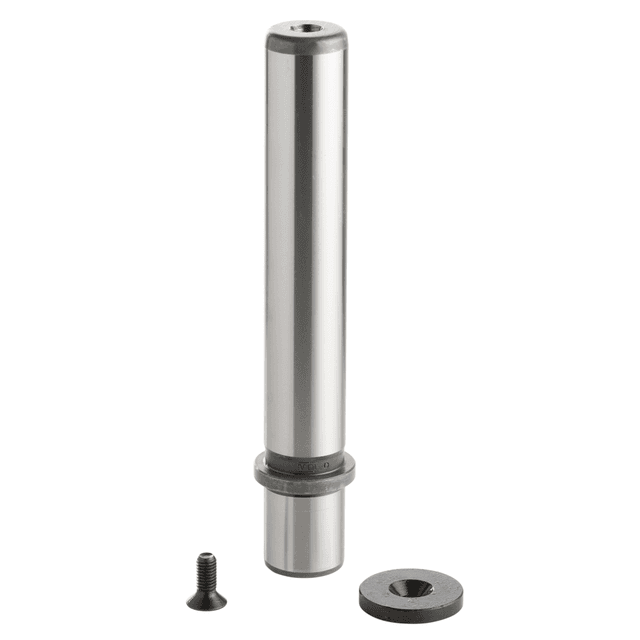
Demountable guide pillar with central fixing DP22 - DIN 9825
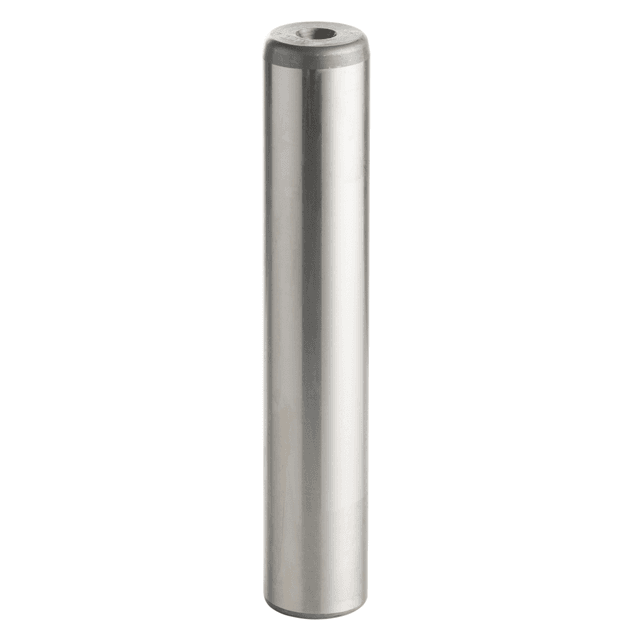
Guide pillar DP10 - DIN 9825
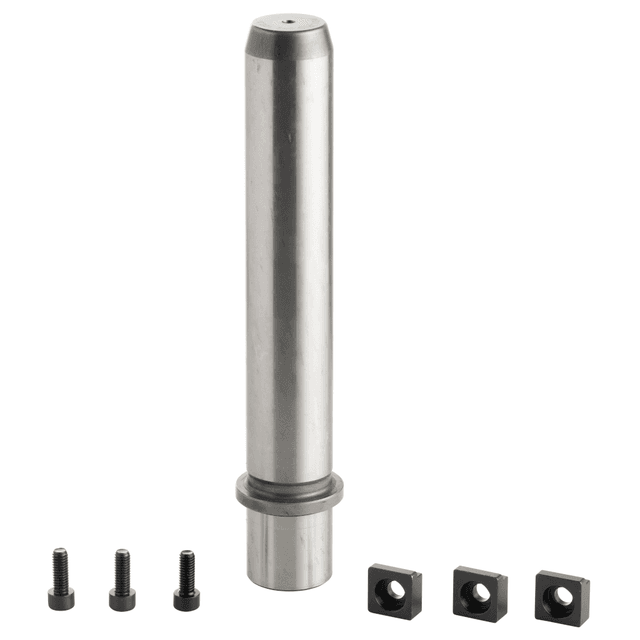
Demountable guide pillar with mounting clamps RID - NF E63-058
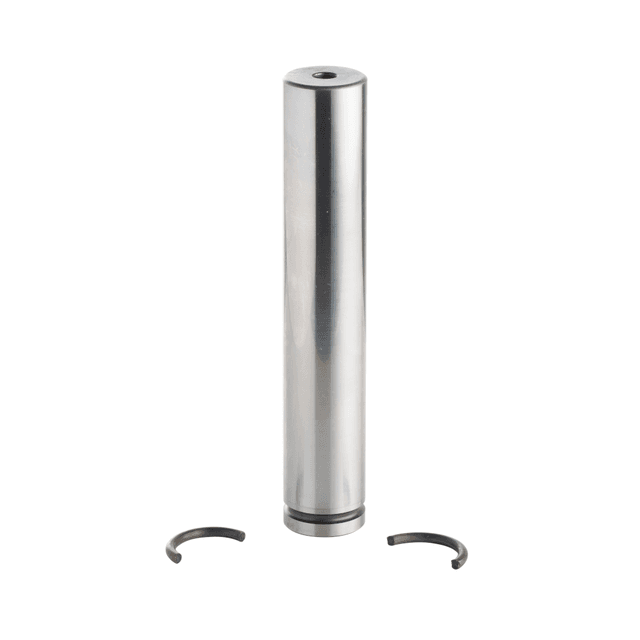
Guide pillar BA - NF E63-120/121
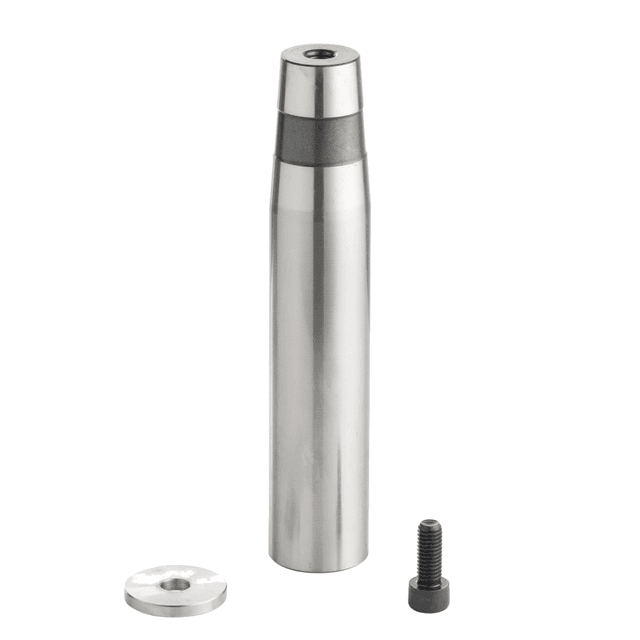
Conical guide pillar CA - NF E63-120/121
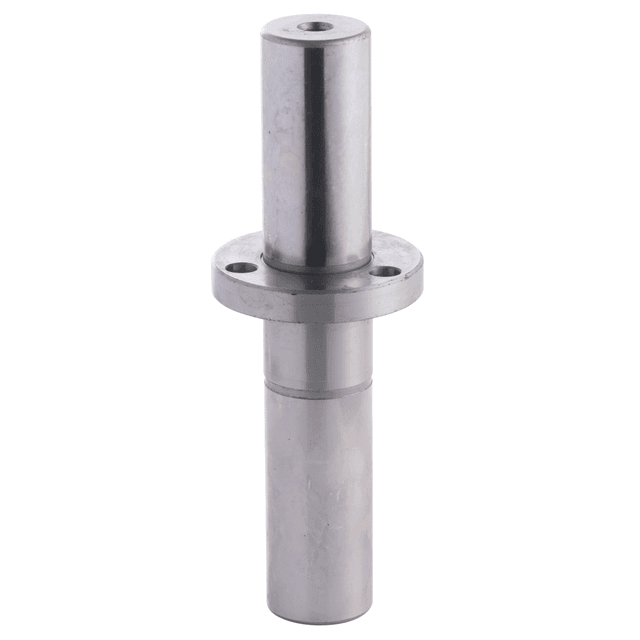
Demountable guide pillar with retaining collar EPO
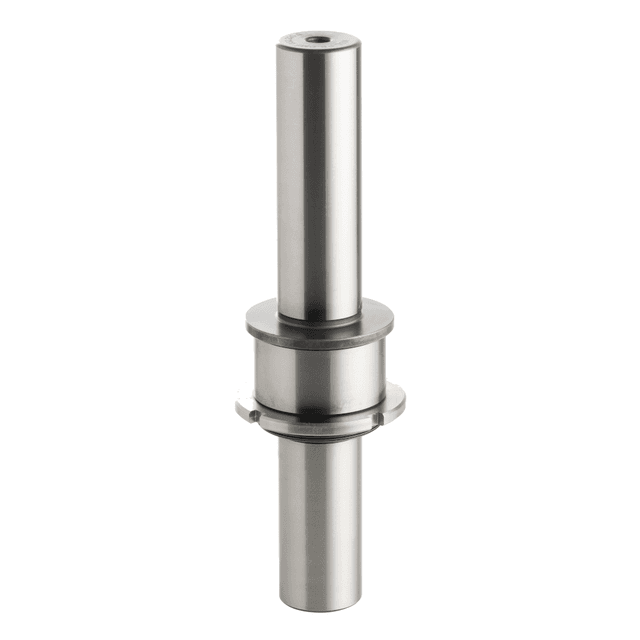
Threaded middle guide pillar CMF
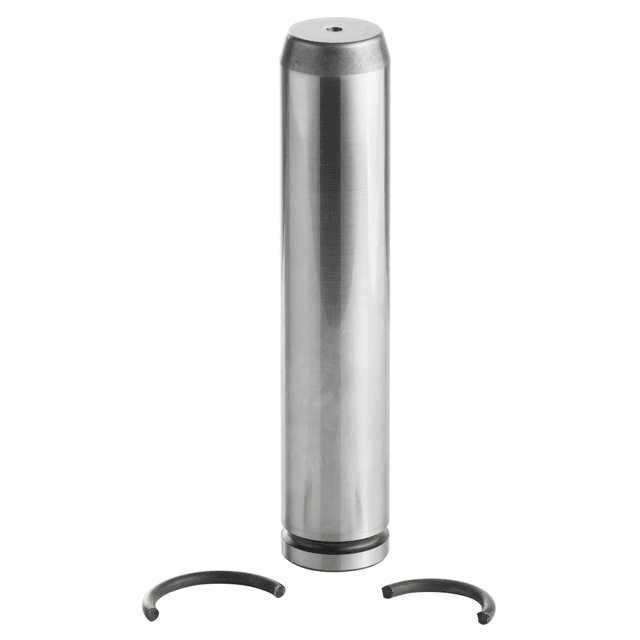
Guide pillar with lower snap-ring clamping RI - NF E63-050
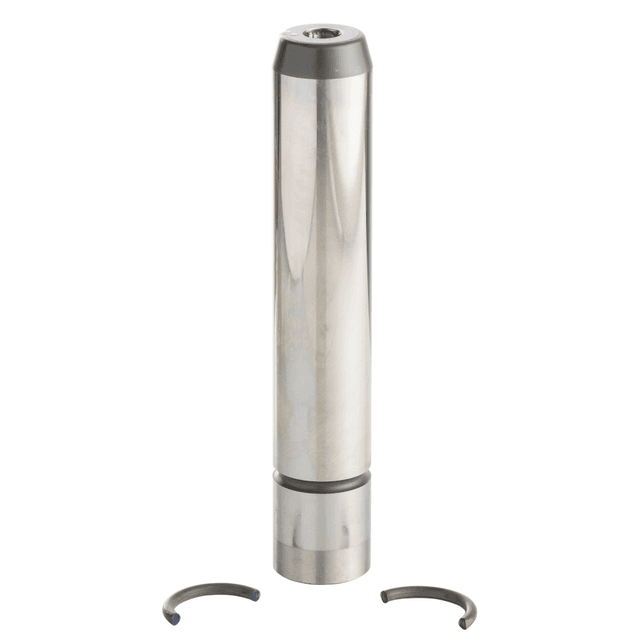
Guide pillar with medium snap-ring clamping RM - NF E63-051
Pillars for every application
Our extensive selection of guide pillars covers all possible applications. Different types cater to diverse needs, such as wear resistance and durability, quick changeovers, radial forces mitigation...
AMDL has a wide range of products to answer any demand, addressing technical challenges associated with each use. This includes smooth, flanged, tapered, center retained, and bottom retained pillars.
AMDL's guide pillars standards
Our guide pillars are sorted into three different groups according to various French, German, European, and international standards:
- MDL PB Range - AFNOR - CNOMO Standard
- MDL Blueline Range - DIN Standard
- MDL Range - ISO Standard
Most guide pillar needs can be met by our extensive in stock collection.
In stock diameters and lengths
Standard guide pillar diameters include: 12 mm, 16 mm, 20 mm, 25 mm, 30 mm, 32 mm, 40 mm, 50 mm, 63 mm, 80 mm, and 100 mm.
Standard guide pillar lengths include: 80 mm, 100 mm, 125 mm, 160 mm, 180 mm, 200 mm, 224 mm, 250 mm, 315 mm, 355 mm, 400 mm, 450 mm, and 500 mm.
We can also provide specific guiding elements for special dimensions.
Pillars for plain or linear ball guides
Our guide pillars can be used in traditional guiding systems with steel or bronze bushes, as well as in ball guidance systems depending on requirements.
Plain linear guide system
Plain guidance of a press tool involves the use of bearing surfaces without rolling elements, ensuring smooth and even movement. In this context, the guide pillar guarantees stability and precision in tool movement, minimizing friction and ensuring optimal alignment for efficient and precise pressing operations.
Plain guide system
Ball guidance of a press tool uses balls to reduce friction and facilitate linear movement of the tool, ensuring high precision and fluidity in faster operating conditions.
The guide pillar, when mounted with a ball cage and bush, forms the basis of this arrangement, allowing stable and precise movement of the die set, which is crucial for high-frequency stamping tools.
Grinding and superfinishing
Superfinishing through grinding enhances the guide pillars' precision by creating ultra-smooth and perfectly aligned surfaces. The roughness is optimal with Ra = 0.2. This reduces friction, increases durability, and optimizes linear movement, essential for precise and fluid industrial operations.
Guide pillars guarantee your tool's perpendicularity
Grinding the pillar's working part and the surface under its collar (easyfit system) ensures precise perpendicularity, guaranteeing optimal alignment between components. This reduces wear, improves stability, and enhances the quality of pressing operations by ensuring smooth and precise movements.
Column hardness
The hardening process, resulting in a hardness of 64 HRC for the pillars, ensures exceptional wear resistance due to the reinforced crystalline structure. This essential property extends the pillars lifespan, making them ideal for demanding stamping applications and prolonging their operational life.